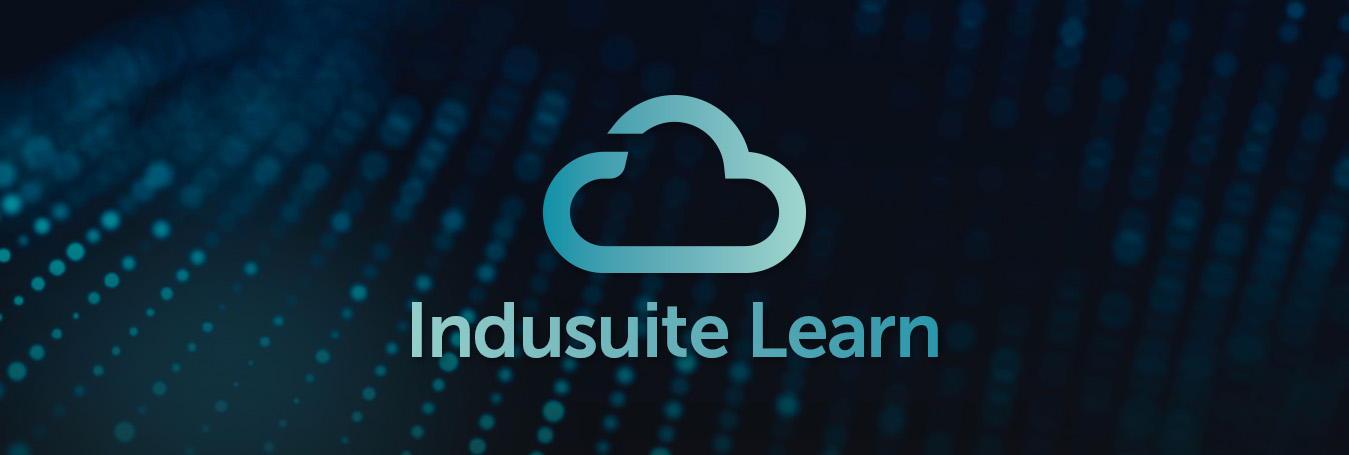
Offline Robot Programming - How This Digital Solution is Helping Manufacturers Increase Their Profitability
How Manufacturers Can Benefit from Offline Robot Programming (OLRP)?
With an almost 12% annual growth, Offline Robot Programming is rapidly advancing and being adopted in the manufacturing industry.
Among the most critical advancements in industrial robotics are the evolution and rapid innovation in Offline Robot Programming (OLRP) and its embracement by the manufacturing industry.
From an era when robots were expensive, exclusively used for one function, and required skilled programmers to the present-day integrated setups that are versatile, agile, and affordable for small and medium enterprises, OLRP software has come a long way.
Unsurprisingly, the OLRP market is expected to grow annually by 11.4% CAGR from 2023 to 2030.
OLRP has proven to be an effective digital solution for manufacturers utilizing robots on their shop floors.
Even with a few challenges that plant managers or integrators may have to encounter, this easy-to-implement digital solution has made an overwhelmingly positive impact on the profitability of companies with several documented success stories.
Benefits of Implementing OLRP into Robotic Workflows
Deploying OLRP in the workflows of industrial robots consistently results in increased productivity.
Simple implementation, scalability, cost-effectiveness, and minimizing downtime are some of the other advantages manufacturers receive by applying this digital solution.
- Boosts Robot's Return on Investment
OLRP is perfect in a high-mix, low-volume production environment such as welding. It improves a robot’s capacity to work on short-run operations, thereby enhancing its ROI. - Reduces Robot Production Downtime
Unlike traditional online programming, OLRP enables industrial robots to be programmed virtually. What used to take days to develop or redesign applications for the robot are now done in a fraction of the time, and without taking it offline and halting production. Result? A significant reduction in downtime. - Makes Programming Easier and More Flexible
Regardless of the brand and configuration, brand-agnostic OLRP solutions offer a single platform for programming complex robot applications within the virtual cell. The digital solution also allows for robots to be reprogrammed and deployed quickly to new tasks, further minimizing downtime. - Validates Designs and Minimizes Errors
Ever wished to develop a proof of process and concept before running an industrial robot on the production floor? Or wondered how to detect and solve problems concerning collisions, joint and reach limits, or discrepancies in CAD?
OLRP enables a real-world simulation by replicating the actual manufacturing cell and creating a ‘digital twin’. This allows the technicians to program in the virtual world to validate new processes and ideas.
OLRP also allows the plant engineer to discover and debug any program errors before robot-specific code is generated to run on the real system.
Similarly, for any differences between a CAD model and its real part, OLRP offers potential solutions to add parametric components to the program to simulate the missing geometry.
- Lowers Costs
As noted earlier, OLRP has a relatively shorter learning curve to learn and design applications. It’s important though that the OLRP platform is proprietary and exclusively built for robot programmers. OCTOPUZ is a great example of such a digital solution that was developed with a specific focus on programming robotic applications offline.- A proprietary solution is more likely to have relevant and impactful features and more valuable updates in the long run.
- Solutions primarily focused on other processes, such as full factory simulation, tend to have crowded user interfaces and include OLRP as one of many software features. This makes it difficult for programmers to create efficient and error-free robot programs.
- Equally importantly, proprietary-built platforms are more economical since they only contain features specific to use cases.
OLRP Applications and Case Studies
OLRP is ideal in industries that are welding-intensive and produce high-mix, low-volume goods. Often, these industries operate in heavily saturated markets and constantly look for ways to stay competitive.
Agriculture, heavy equipment and fabrication shops are among the industries OLRP is successfully deployed.
Pro-tip for interested buyers: Look for a software platform that supports all kinds of robotic welding including MIG and TIG welding, spot welding, and tack welding.
It’s also vital to have other features:
- Autonomous and intuitive weld creation
- Automatic finding of the start and end of welds
- Automatic calculation of external axes based on user-selected torch orientation
One such OLRP software is OCTOPUZ which has vast experience and numerous success stories with welding-intensive companies.
Flory Industries, a nut-harvesting equipment manufacturer, used OCTOPUZ to program a Fanuc robot in their welding cell in order to weld components for their harvester machines.
FANUC Robot Programmed with Flory Industries - YouTube
OCTOPUZ enabled them to easily create weave and stitch welds, allowing the robot to reach all areas of the parts to be welded and achieve constant push angles.
Another company, York Metal Products, used OCTOPUZ to program their KUKA robot arm to reduce their programming time and robot downtime for arc welding.
York Metal Products KUKA Weld Cell On-Site Implementation | OCTOPUZ
Welding aside, OLRP is also used in other applications:
- Cutting
- Spraying and Painting
- Additive Manufacturing
- Machining
Even though employing OLRP offers several benefits across industries, there are a few challenges that programmers and technicians must work through to get the most from their OLRP software.
Challenges with OLRP
It is imperative for the virtual world in the OLRP software environment to match real-world conditions. This means the components should be aligned with proper variables in exact locations. A ‘mastered robot’ ensures that it works as expected in reality too.
Shop floor engineers would additionally want robot backup files from the actual robot so as to understand the distinct options and code structures crucial in robot code generation.
Hence, it is important to choose a reputed software provider that offers remote or onsite implementation services and ensures its software works well for the clients.
To avoid touch-ups post-processing, the Tool Center Point (TCP) that defines the exact working point of the robot, along with the User Reference System, needs to be correctly set before executing a program.
The robot will also benefit from accurate touch sensing, vision systems, and seam tracking to locate the right places and carry out its intended activities.
Lastly, as they say in the industry, an OLRP software is only as good as the CAD. Thus, having precise and high-quality CAD is essential.
Aside from return on investment, increased accuracy, and decreased downtime, OLRP also addresses the constant labor shortages in the market. It has been a boon for engineers, technicians, and plant managers and has enabled business owners and the overall manufacturing industry to be more competitive.