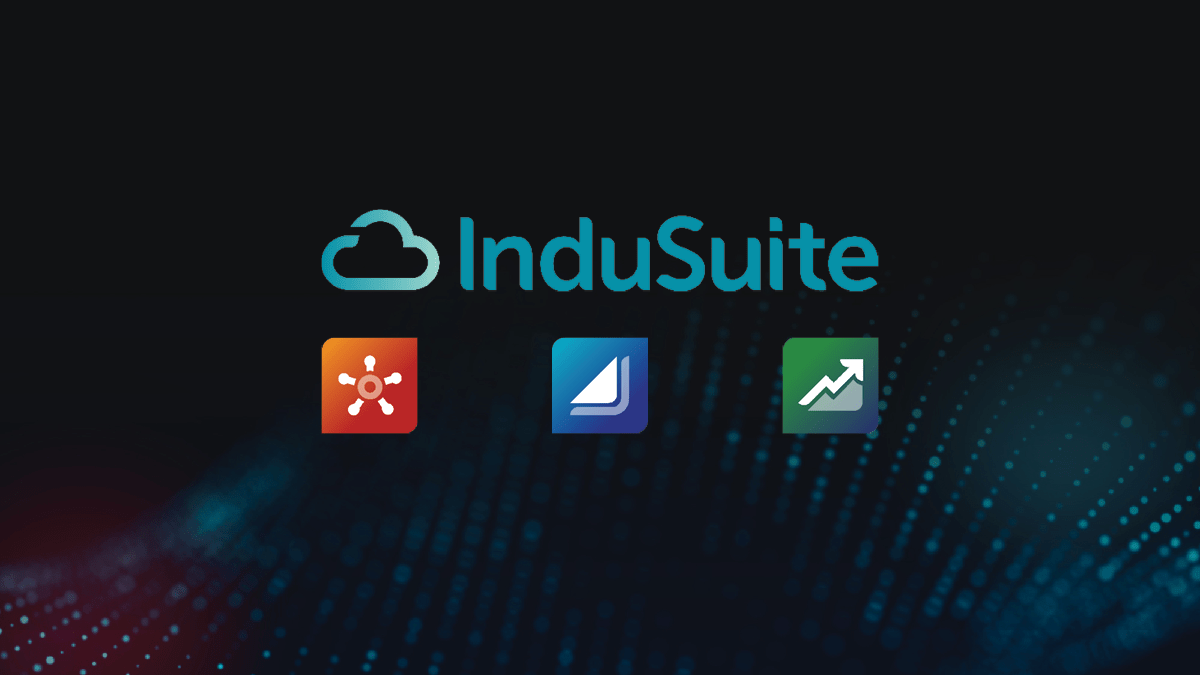
7 Ways Digital Weld Tracking Can Improve Productivity
Boosting Productivity: 7 Ways Digital Weld Tracking Revolutionizes Operations
Digital weld tracking has emerged as a game-changer, revolutionizing the way welding operations are managed and monitored. By leveraging advanced technology, these systems significantly enhance productivity – here are 7 of the biggest ways how…
1. Faster Documentation Management
Traditionally, managing and organizing welding documentation has been a time-consuming and error-prone process. Digital weld tracking systems streamline this task by providing a centralized platform for storing, organizing, and accessing critical welding data. With a few clicks, welders, inspectors, and project managers can easily retrieve information related to welding procedures, specifications, and quality control records. This quick access to documentation significantly reduces administrative burdens and allows teams to focus more on actual welding tasks, saving time and improving overall productivity.
2. Fewer Re-welds
Re-work due to weld defects can be a major setback, leading to wasted time, materials, and labor costs. Digital weld tracking systems help minimize re-work by enabling real-time monitoring of welding parameters and quality metrics. By continuously capturing and analyzing data during the welding process, these systems can detect potential defects early on, allowing for immediate corrective action. The ability to identify and address issues promptly helps reduce the number of re-welds required, ensuring that projects progress smoothly and efficiently.
3. Enhanced Welder Performance
Digital weld tracking systems empower welders with real-time feedback and performance metrics. By monitoring parameters – such as amperage, voltage and wire feed speed – these systems provide valuable insights into welding technique and quality. Welders can use this information to optimize performance and compliance to welding procedures, make necessary adjustments, and achieve consistent and high-quality welds. The ability to monitor and improve welder performance not only boosts productivity but also enhances the overall quality and reliability of welded structures.
4. Improved Subcontractor Performance
For projects involving multiple subcontractors, co-ordinating and managing welding operations can be a complex task. Digital weld tracking simplifies subcontractor management by providing a unified platform for collaboration and data sharing. Real-time visibility into subcontractors' progress, welding procedures, and quality control measures enables efficient coordination and ensures adherence to project timelines. This improved subcontractor performance eliminates delays, rework, and communication gaps, leading to enhanced productivity and successful project outcomes.
5. No Missed Qualification Deadlines
Welding certifications and qualifications are essential for ensuring the competence and reliability of welders. However, managing the expiration dates and renewal processes of these qualifications manually can be challenging and prone to errors. Digital weld tracking includes built-in qualification tracking features that automatically notify weld managers and welders well in advance of upcoming qualification deadlines. This proactive approach eliminates the risk of missed deadlines, ensuring that welders maintain their qualifications and can continue working without interruptions.
6. No Wasted Resources Re-Qualifying Welders
When welders' qualifications expire, re-qualifying them can be a time-consuming and costly process. Digital systems streamline this process by providing a comprehensive overview of welders' qualifications and their validity status. With this information readily available, supervisors can efficiently plan and schedule re-qualification activities, avoiding unnecessary downtime and the wastage of resources. By simplifying the re-quslification process, these systems contribute to heightened productivity and cost-effectiveness.
7. Lower Risks Of Weld Failure
Weld failures can be catastrophic and have severe consequences. These tracking systems help mitigate these risks by monitoring critical welding parameters and quality metrics in real time. By detecting deviations or anomalies during the welding process, these systems alert operators, enabling them to take immediate corrective action. By proactively preventing weld failures, digital weld tracking systems contribute to increased productivity and significant cost savings associated with re-work, repairs and liability.
Fundamentally, digital weld tracking systems enhance productivity by optimizing processes and minimizing risks. By embracing the power of technology, welding professionals can unlock substantial gains in efficiency, quality, and project success. Why not try for yourself?
Book a free WeldCloud Notes demo now.