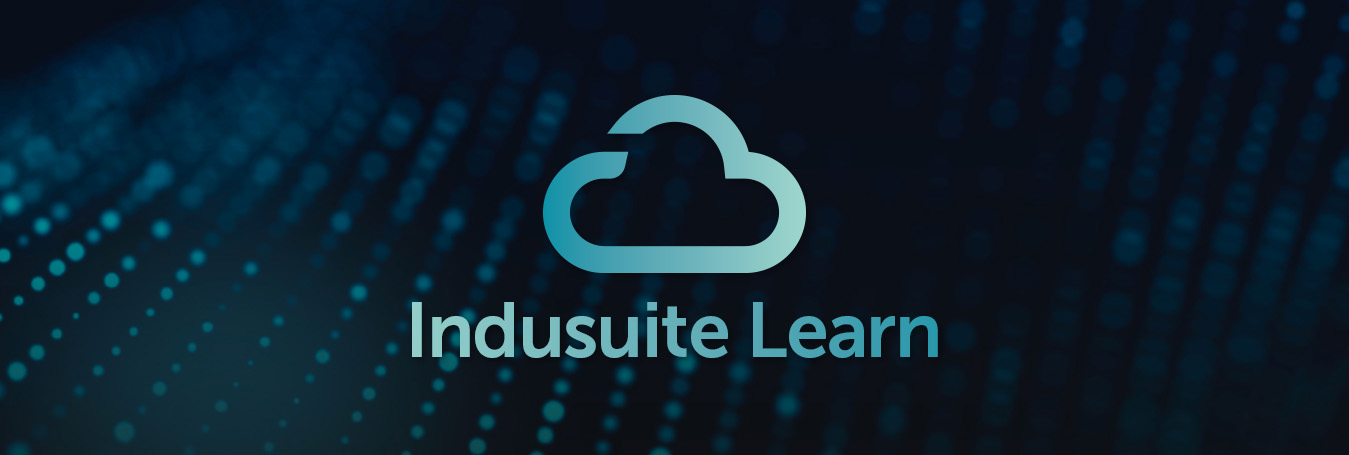
Tips and Tricks for Optimizing Your Cutting Workflow with Automatic Nesting
How Digital Solutions Improve Productivity and Efficiency
Manufacturers transition to automation for higher efficiency and quality in their cutting. Optimizing this new cutting workflow is critical for operations of every size. Whether in a small shop with one cutting machine or a large shipyard processing multiple projects each day, there are ways to ensure each step of the cutting process is performed to the highest level of productivity.
So how can operators easily identify bottlenecks in planning or production? What steps in preparation can be minimized to improve productivity? Let’s explore how digital solutions software, like automatic nesting, helps optimize the cutting workflow.
How to Identify Bottlenecks
The simplest way to see improved productivity is by identifying and resolving bottlenecks across the operation. These are specific points in the cutting process where the workflow is slowed down or delayed, resulting in decreased efficiency and lower quality.
Bottlenecks may be present anywhere in the operation. By understanding what hinders a cutting workflow from operating at maximum efficiency, manufacturers can resolve issues at the source.
Planning Bottlenecks
Bottlenecks often hinder production time before the first cut is even made. Order transfer, importing files, drawing, and nesting can cause a backup in production. These issues tend to compromise workflow and minimize overall productivity. It is critical to address each problem and make the planning stage a seamless process.
Production Bottlenecks
Eliminating bottlenecks in planning is only half the battle. To truly optimize the cutting workflow, manufacturers must identify and resolve bottlenecks after production begins. Where is valuable time lost? These delays and bottlenecks in production can be caused by a variety of factors.
Are machines waiting while a plate is manually nested? Is there an issue with the cranes or moving plates? Is the final product not up to standards? These are just some of the factors that reduce the overall productivity of an operation and must be addressed.
So how do you know what specific issues are hindering productivity once production begins? Digital solutions can provide an analysis of production and identify productivity bottlenecks. Applications like CutCloud cutting management software use data to paint a full picture of the cutting process and pinpoint specific problems. Managers can then use this data to resolve the bottlenecks in each stage of production and achieve higher productivity and efficiency across the board.
How to Minimize Preparation and Planning Time
After identifying potential bottlenecks and time-wasters, managers can take the next step in optimizing their cutting workflow - minimizing time spent in preparation and planning.
Before a single cut is made, each piece must be nested. This involves efficiently arranging the individual parts on a sheet or plate in preparation for cutting. The goal of nesting is to maximize material utilization while minimizing waste.
So how can you optimize the nesting process and minimize planning time? Simply put – there is nothing faster or more efficient than automatic nesting. It significantly reduces the time required for nesting parts on a plate and frees up workers for other tasks. This process that may have required hours to complete manually is now achievable in just minutes - or even seconds! In some cases, automatic nesting results in up to 90% time savings across cutting operations.
Automatic Nesting for Smaller Productions
Smaller productions can benefit from automatic nesting even if the full operation only involves one cutting machine or minimal cutting tasks. By decreasing the time and resources spent on nesting, operators increase overall efficiency and make the most of equipment and worker capacity.
But how can smaller productions take advantage of automatic nesting without installing a full, complex system? Cloud-based software like EasyNest Online offers an easy-to-use solution for standard cutting machines that does not require the hassle or investment of hardware. This application allows users to import part geometries, determine the quantity to be processed, and define material and nesting settings. It then uses industry-leading algorithms to nest faster, utilize less material, and deliver the best cut possible.
While cloud-based software like EasyNest Online may not feature all of the capabilities available in more robust CAD/CAM systems, it is a helpful and necessary tool for smaller productions looking to ensure the cutting process is set up correctly and optimized.
Automatic Nesting for Larger Productions
The capabilities and benefits of automatic nesting significantly increase for larger productions. More machines in the workflow and higher cutting capacities offer plenty of opportunities to see the value of automating the planning and preparation processes.
CAD/CAM systems like COLUMBUS provide a more complete workflow solution and aid in the process of setting up the entire operation correctly. The software handles complete assemblies, not just single parts. With more functionality overall, manufacturers can handle everything from order processing and file imports to direct drawing transfer and nesting all in one program.
Get Started with Automatic Nesting
While there will always be a need for a human touch to tweak and control different aspects of the cutting operation, automatic nesting reduces the hands-on approach by providing valuable insights that can be used to optimize the process.
Ready to get started and improve your operation’s overall productivity? The InduSuite team is here to help you find the right solution for your unique cutting workflow. Get started today!