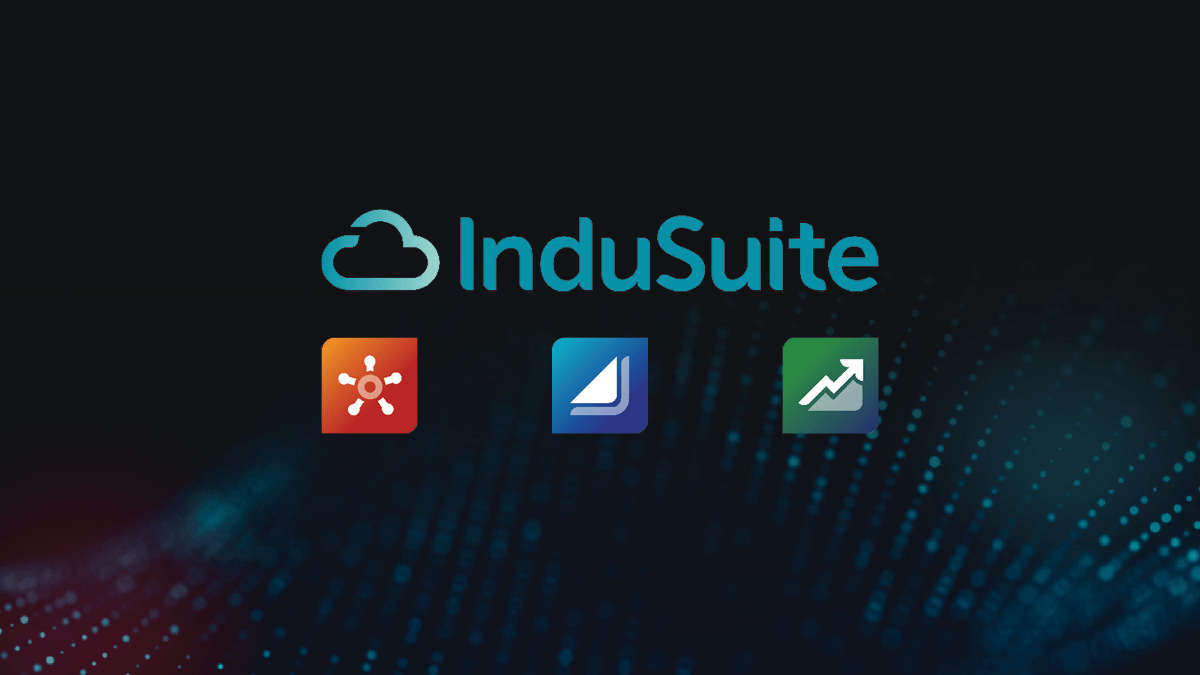
Embracing the Digital Era with Weld Tracking
Weld Tracking: Is This the Right Time to Go Digital?
Welding is an art, demanding subtle skills to deal with an infinite combination of dimensions, materials, specifications and tools. Attempts to turn it into a science, to measure and codify its multiple aspects, are fraught with difficulty.
At the same time, however, modern industry demands data, transparency and accountability. InduSuite spoke to Tiago Pereira, a welding software developer, about why the time is right for welding to go digital.
What is Weld Tracking?
Weld tracking, or weld mapping, is the concept of digitalising all the information about a weld. Some of that information is mandatory even to start a project — you cannot simply sign a contract and start welding.
Weld tracking is only necessary for certain types of structures. If you are welding gates in a residential neighbourhood, you don’t need these kind of records. At the other end of the scale, if you are welding super austenitic stainless steel piping for a nuclear plant, you definitely do.
Why is So Much Detail Required?
Welding mistakes can be catastrophic. Take Thunderhorse, the BP oil rig that nearly capsized in a hurricane in 2005. The subsequent investigation showed it was due to welds that didn’t have the proper procedures. The company spent hundreds of millions of dollars on rewelding, and narrowly avoided crippling fines. If they had put the proper procedures in place, they would have saved this money and reputational damage – it could all have been avoided.
In recent years, welding failures have disrupted railways, brought down cranes, and set ships adrift. Lives depend on accurate welds. A turbine, a ship’s hull or a building in an earthquake zone – get the cooling rate wrong and the weld will be weak. This is why a welding bureaucracy has emerged to draw up international standards and police them.
Whose Responsibility Is All This?
Quality department managers, welding engineers, and even managing directors, need to know how the welding bureaucracy works. Writing a WPS is one thing, but navigating the bureaucracy – making sure all the right boxes are ticked – is on another level.
Weld tracking doesn’t help the welder operate his tools. But an important part of the equation is the welding engineer, the guy who defines the procedures and processes, who sets the parameters of the weld. The welder has the technique, not the overall knowledge. Welding engineers rely on having the right procedures in place.
What Does Software Do That Excel Can’t?
The software compares the parameters and variables that define a project with all the data stored in your PQRs. You just click on a button and it tells you any gaps you need to fill. Companies that don’t have this tool – in other words, most of them – will have an Excel sheet with hundreds of entries, one for each PQR, and they have to search each parameter. This takes a lot of time, is stressful and is far more prone to error.
Our industry changes slowly, connectivity is only just getting started and most companies still track welds manually. But Industry 4.0 is the future, and for welding it means investing in digital.
How Big is the Investment?
The biggest problem is migrating existing PQRs into the system. There is no accurate way of transferring the data into the software apart from manually. Importing data directly from an Excel spreadsheet is never reliable. With that important caveat, however, the software uses the industry terminology, so it is straightforward – if time-consuming – to fill in the drop-downs yourself. But that is a one-off investment.
The learning curve is not a significant obstacle. It doesn’t require a lot of training, the buttons are clear and self-explanatory – that’s the feedback we have. For WeldCloud Notes, for example, we have a “chat” facility on the website, but users very rarely need any help. The main thing is simply changing the status quo: “We’ve done this for 30 years, why change?” Once you trial the software, the “aha” moment comes quickly, when the penny drops and people grasp the potential for what the software can do. It saves time.
What Can Weldcoud Notes Do That Other Weld Tracking Software Can’t?
We devised a matrix that includes all the pipe diameters and schedules, plus each PQR, welder certificate, WPS and so on. You select the different pipes or plates that are going to be welded, you set the base material, positions, preheat and/or postweld heat treatment temperatures (and other variables), then by clicking on a button all these parameters are compared with your documentation.
The matrix serves as a summary of your company’s qualifications for the job. We have called it the Q-Matrix, and it tells you all the PQRs that are relevant to a specific weld. And rather than taking days, you can do it in 20 minutes. This has turned out to be a major time-saver for our clients, the welding engineers and welding coordinators. It makes the searching so trivial that they don’t hesitate to do plenty of searches.
What Can’t It Do?
At the moment we can’t make the link between the welding power source and the weld documentation aspect of the software, but we are currently working on a product that will enable this feature for our customers.
Apart From Saving Time, are There Other Benefits?
There are multiple benefits to digitising your weld tracking, including traceability, communication, documentation and compliance – not to mention the peace of mind that comes with this clarity. The productivity gains are clear, for example:
• Documentation management
• Fewer re-welds
• Improved welder performance
• Improved subcontractor performance
• No missed qualification deadlines
• No wasted resources re-qualifying welders
• Lower risks of weld failure.
We will go into more detail in subsequent articles on InduSuite.com.
Click here to schedule a free demo.