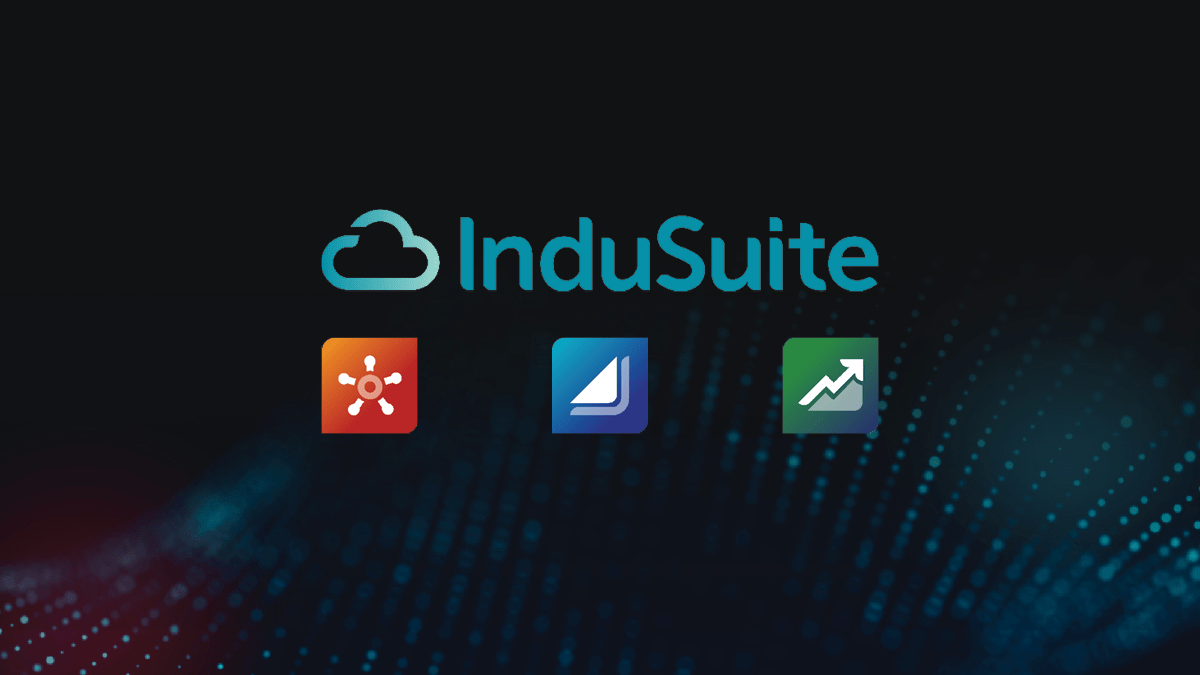
Why a Petrochemical Giant Braskem Chose Digital Weld Tracking
Transforming Weld Quality: How Braskem, a Petrochemical Giant, Embraced Digital Weld Tracking
Trying to manage hundreds of thousands of welds manually was a huge task for Braskem, the world’s eighth-largest petrochemical company, leading to mistakes, costly rework, and leaving them open to liability. Could digital weld tracking help boost quality?
“ We didn’t have a system to handle all the documentation. We didn’t have any transparency on the information that we received. We only had a huge stack of papers that were dropped on my desk to be reviewed.”
For Braskem welding engineer, Luis Greggianin, the problem was familiar. In a highly risk-conscious and audited industry, piles of paperwork were the norm.
As the largest petrochemical company in Latin America and the eighth largest worldwide, Braskem works with multiple subcontractors to supply welding services and employs a team of weld inspectors, welding engineers, and quality assurance personnel to monitor and manage them.
But with hundreds or thousands of welds every week to document manually, traceability and quality were suffering.
Luis explains: “There was not enough testing or traceability, so our subcontractors would end up sometimes cutting out and redoing the weld. We experienced approximately two rewelds a day, and that’s too much rework, too much time, and too many delays.”
Something had to change.
A Modern Platform, the Best Solution
The answer for Braskem was ESAB’s WeldCloud Notes. The digital software platform is accessible from any web-enabled device, is password-protected, and provides a suite of tools and dashboards.
Ideal for welding engineers, reliability managers, and quality personnel, WeldCloud Notes streamlines the documentation and reporting process by completing four essential tasks:
- Maintain quality and compliance while managing PQR and WPS documents in one place.
- Efficiently review all PQR, WPS, and WPQ information with a quick and easy search.
- Generate a PQR or WPQ with all of the essential variables.
- Avoid a missed qualification deadline or wasting resources requalifying welders.
Users can track the productivity of individual welding systems and welders, register weld seam data, and manage the calibration records for an entire fleet of welding machines.
As an online software tool, any relevant person on a project can access information (with restrictions specified by the administrator), search for the correct PQR and WPS, introduce welding records, keep track of production, and print reports for all the activity completed.
As Luis notes: “WeldCloud Notes had all the features that we needed and was the most modern platform, so we decided this was the best solution.”
Verify Every Weld
Weld tracking software drives up quality because of the huge improvements it makes to traceability, documentation, communication, and compliance.
Before implementing WeldCloud Notes, Luis estimated that failure to comply with the WPS caused 30% of the rework cases, while poor supervision, visual inspection, or NDT practices caused the other 70%.
WeldCloud Notes accurately communicates the WPS, non-destructive testing (NDT) methods, and NDT documents to field teams, and test results are immediately available for real-time assessment.
And while the software can’t carry out inspections, Luis says that operators now understand that the weld has to be done properly and exact procedures must be followed.
“Overall, they’re happier because they hate doing rework,” he says. “Everyone involved in the welding processes is more determined to do it properly because of the added scrutiny.
“WeldCloud Notes software allows us to monitor welds very quickly. We can identify the status of a weld — in fit-up, welded, tested, or processed and complete — from any location. We don’t have to wait for field reports. With the software, we can now verify the company and operator responsible for every weld seam.”
Reports in Minutes
Because the petrochemical industry is highly audited, Braskem spends a significant amount of time on compliance. A data book of all weld info for an average project runs into 1,000+ pages, taking days to compile the scattered information and track down the right people.
“Before WeldCloud Notes, generating a data book of 600 welds for the customer would take one to two days — now it takes 5 to 10 minutes.”
Continue reading about Braskem and WeldCloud Notes.
Book a free WeldCloud Notes demo.