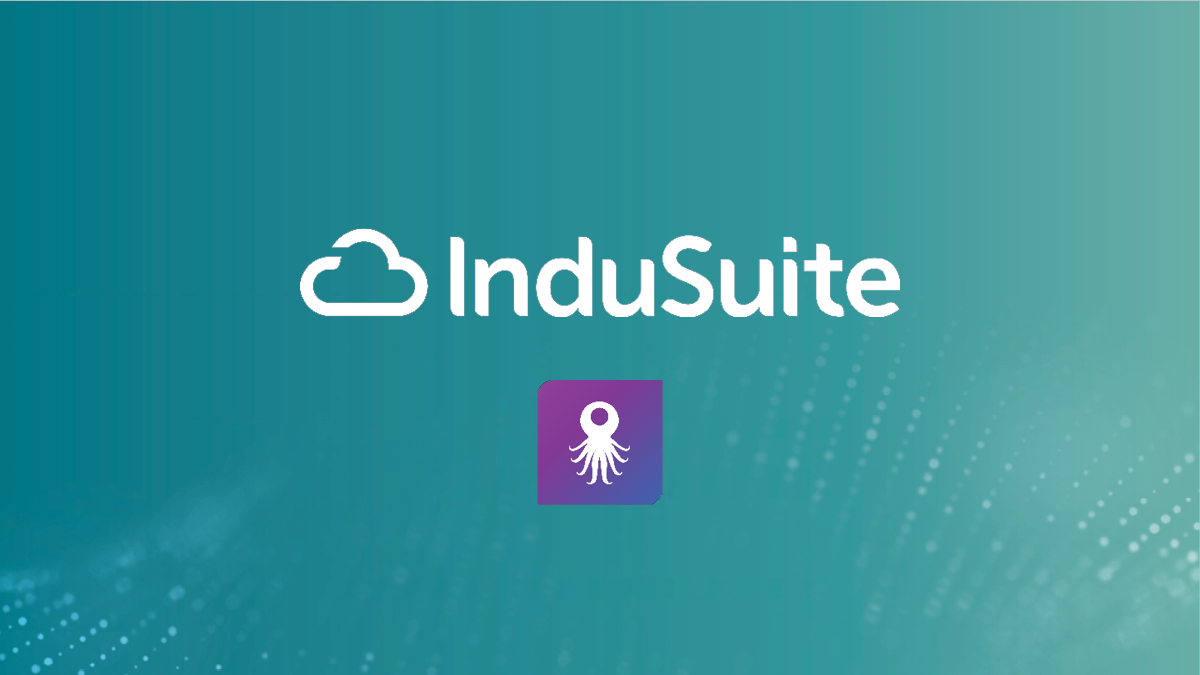
How OCTOPUZ Translates Improved Workflows Into Calculated Savings
Translating Improved Workflows into Calculated Savings
When manufacturers implement robotics into the fabrication process, there is already a demonstrated desire to enhance overall quality and experience efficiency in the operation. The ability to improve a robot’s capacity to work in a high-mix, low-volume environment like welding is critical for maximizing its return on investment (ROI).
Offline Robot Programming (OLRP) is designed to be the next step in the journey. But is the investment of time and money into OLRP actually worth the cost?
In this article, we’ll explore how OLRP streamlines workflows and helps users scale their robotics operations while experiencing true cost savings.
Streamlining Workflows with OCTOPUZ
Maximum efficiency equals tangible cost savings. OCTOPUZ from InduSuite is a comprehensive OLRP software solution for robotics that enables fabricators to program robots in an offline environment, identify inefficiencies in production, prevent potential robot errors, optimize overall production cycles, and make data-driven decisions that maximize the efficiency of the robotics equipment.
How do these capabilities actually impact the bottom line of a manufacturing operation?
Reduced Downtime
Valuable welding time is lost every time a robot is removed from production for programming. In some cases, traditional programming may take multiple days. It all depends on the complexity of the program.
OCTOPUZ cuts this programming time in half . With OLRP, robots continue welding using the previous set of parameters while programmers update and reconfigure settings in an offline environment. Full robot programs are created and implemented without removing the robot from production. This ability to view accurate simulations and easily program settings offline greatly reduces setup time for new tasks or changes in an operation.
An additional way to decrease downtime is to have a better understanding of how long a process will take once implemented. The timing affects scheduling and production for the entire
operation. With OCTOPUZ, users can calculate the cycle time instantly and optimize the project before welding begins.
Error Prevention
Errors are costly. Even a minor miscalculation or programming error can result in massive damage to the robot or the workpiece. These errors prove even more costly if the material is expensive or scarce.
One of the proven ways to improve workflow and see actual cost savings is to eliminate errors in the programming stage. By simulating entire welding programs in an offline environment, programmers can review any potential issues in the code and make all required adjustments before implementing it into the robot.
Accelerated Training
Training users on new software takes away from the time they could be on the production floor. OCTOPUZ reduces the learning curve and accelerates the overall training time for programming. It provides an offline environment for users to program and simulate operations without direct interaction with the robot.
With easy-to-use software and enhanced training capabilities, there is an opportunity to increase the number of trained operators within a company. More proficient programmers lead to more productivity and improved workflow.
Scaling Digital Solutions for Cost Savings
Robotic welding operations are always changing, and production requirements shift with the needs of customers. Implementing OCTOPUZ isn’t just a one-and-done solution. There are plenty of ways to maximize the effectiveness of OLRP across a fabrication operation.
Brand-Agnostic Coding
An additional benefit to brand-agnostic software is the freedom to choose equipment based on application requirements, rather than limiting only to existing shop equipment. OCTOPUZ provides a single platform for all brands, allowing users to program multiple robots, configurations, and applications from a single software.
But isn’t there a different code for each robot brand? Of course. OCTOPUZ is designed to bridge the gap between robot brands. It produces identical programming based on unique configurations up until the point where the robot’s code is actually created.
This cohesiveness allows for more production time and fewer scheduling headaches. With programming no longer limited to those familiar with specific robots, managers can schedule effectively and enhance overall productivity across the operation.
Full Integration with InduSuite
There are also ways to incorporate applications into other aspects of the fabrication process. OCTOPUZ is part of InduSuite - a brand-agnostic ecosystem of digital welding, cutting, and robotics solutions.
InduSuite offers additional applications for welding and cutting, including:
- WeldCloud Productivity - Welding Productivity Analysis
- WeldCloud Notes - Welding Documentation
- WeldCloud Fleet - Welding Fleet Monitoring
- EasyNest Online - Cloud-based Nesting for Standard Cutting Machines
- CutCloud - Cutting Productivity Analysis
- COLUMBUS - CAD/CAM Software
OCTOPUZ and the entire portfolio of applications from InduSuite are valuable investments for any fabrication operation. Manufacturers who want to experience true cost savings must consider digital solutions as a tool to maximize efficiency and get the most out of each piece of equipment in their shop.
Get Started with OCTOPUZ
Ready to experience the cost savings of OCTOPUZ? The team is here to walk through the implementation process and ensure the virtual world created in OCTOPUZ matches what your physical robot system encounters in the real world.
Book a demo today to get started!